A Book on Consignment Inventory System For Hospitals
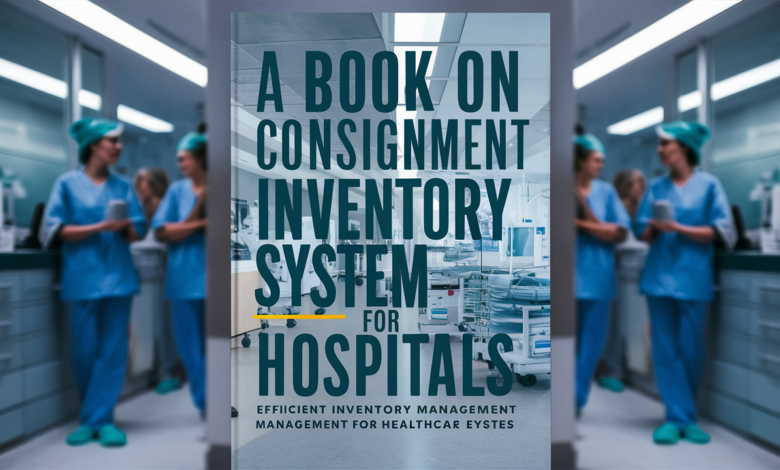
Managing inventory in hospitals can be a daunting task, given the complex nature of healthcare operations and the high demand for medical supplies. Imagine running a hospital and finding out that crucial supplies like surgical instruments or life-saving medications are either running low or out of stock when you need them the most. It’s a situation no healthcare provider wants to face, but unfortunately, it’s a reality many have to deal with. This is where a consignment inventory system for hospitals can make a big difference. Not only can it improve efficiency, but it can also significantly reduce costs and waste. In this blog, we’ll explore the importance of this system, its benefits, and how it works—through personal stories, real-life examples, and more!
What is a Consignment Inventory System?
A consignment inventory system is a method where a supplier delivers products to a hospital, but the hospital only pays for the items once they are used or consumed. The inventory remains the supplier’s property until it’s utilized. Think of it like renting supplies rather than owning them. This method is increasingly gaining popularity in hospitals due to its ability to reduce upfront costs and increase supply chain efficiency.
My Personal Experience with Consignment Inventory
I remember the first time I heard about consignment inventory systems in a hospital setting. I worked at a mid-sized medical facility where inventory management was chaotic. We often had to deal with understocked supplies, particularly in emergency rooms and operating theaters. One day, a colleague shared how their hospital adopted a consignment inventory system and noticed an immediate difference. They had access to the necessary supplies at no initial cost, and the suppliers replenished their stock automatically when it was running low. It wasn’t just about having supplies available but also about easing the financial burden of managing them.
Seeing the difference in how things operated at that facility got me thinking: “Why don’t all hospitals adopt this model?”
Benefits of Consignment Inventory for Hospitals
1. Cost Savings
One of the most significant advantages of consignment inventory systems is the reduction of upfront costs. Hospitals often operate under tight budgets, and buying in bulk can strain their finances. By implementing a consignment system, hospitals can lower their initial investment and free up resources for other essential services. The best part? Hospitals only pay for what they use, meaning no unused inventory gathering dust and becoming obsolete.
2. Improved Stock Management
Managing inventory can be time-consuming and error-prone without the right systems in place. A consignment inventory system allows hospitals to monitor stock levels in real time. Suppliers can automatically track how much of their products are being used and send replenishments as needed, ensuring that essential supplies are always available when needed most.
3. Reduced Waste
Hospitals often deal with products that have an expiration date, such as medications and medical supplies. Without proper inventory tracking, it’s easy to let these products expire before they can be used. With a consignment inventory system, products are automatically rotated and restocked before they expire, minimizing waste.
4. Focus on Patient Care
With a streamlined and cost-effective supply chain, hospital staff can focus more on patient care rather than worrying about managing stock levels. Nurses, doctors, and administrative staff can spend less time handling inventory and more time ensuring that patients receive top-notch care.
How Does Consignment Inventory Work in Hospitals?
A consignment inventory system in a hospital involves close collaboration between the hospital and suppliers. The hospital and supplier agree on the terms of the consignment agreement, including which products will be provided and how inventory will be tracked. In many cases, hospitals use specialized software to track usage, and suppliers automatically replenish stock once it falls below a certain threshold.
For example, if a hospital needs a particular type of surgical glove, it can receive a consignment supply from the manufacturer. The hospital won’t pay for these gloves until they are used in a procedure. The supplier is responsible for replacing them once the stock starts running low. This minimizes the risk of stockouts and reduces the hospital’s financial burden.
Challenges and Considerations
While the consignment inventory system offers many benefits, it’s not without its challenges. One common issue is ensuring accurate tracking and monitoring of inventory. For example, if a hospital fails to record usage accurately, it could lead to either overstocking or understocking. Furthermore, hospitals need to maintain strong communication with suppliers to ensure that stock is replenished on time and that agreements are adhered to. A failure in communication could result in shortages of essential supplies when least expected.
Conclusion
The consignment inventory system is changing the way hospitals manage their medical supplies. By reducing upfront costs, improving stock management, and minimizing waste, hospitals can operate more efficiently and allocate their resources to patient care. As healthcare providers continue to search for ways to improve operational efficiency and reduce costs, consignment inventory might just be the solution that transforms the way hospitals approach inventory management. Whether you’re a small clinic or a large hospital, this system offers flexibility, cost savings, and more, helping you deliver better care to your patients.
Frequently Asked Questions (FAQ)
Q1: Is a consignment inventory system suitable for all hospitals?
Yes, consignment inventory systems can be beneficial for hospitals of all sizes. Smaller hospitals may find them especially useful in managing their cash flow and reducing overhead costs. Larger hospitals can benefit from the system’s scalability and improved supply chain management.
Q2: How does a hospital track consignment inventory?
Hospitals typically use software that integrates with the supplier’s system to track usage and stock levels. These systems provide real-time updates, ensuring the hospital and supplier are on the same page regarding inventory levels.
Q3: What happens if a product is damaged or expired in a consignment inventory system?
In most cases, the supplier retains ownership of the inventory until it is used. If a product expires or is damaged before use, the supplier is responsible for replacing it. However, hospitals must have clear terms in place regarding damages and expiration in their consignment agreements.
Q4: Can a hospital reduce its waste with consignment inventory?
Yes, the consignment model helps reduce waste by ensuring that products are replenished only when needed. This minimizes the risk of overstocking and ensures that items are used before they expire.